Today’s offshore wind turbines stand taller than the Boston skyline.
Each blade is about the length of a football field, which means 50 feet have to be cut off to get one inside the state’s Wind Technology Testing Center in Charlestown.That’s where the blade for Vineyard Wind went through strength testing earlier this year.
In a cavernous testing room, the blade is mounted horizontally by the base. A hydraulic piston — making a gentle hiss-hum-hiss sound — moves the blade from below, and weights clamped across the blade add pressure.
It’s kind of like wagging a dog’s tail.
Executive Director Rahul Yarala said it simulates the stress of real-world conditions.
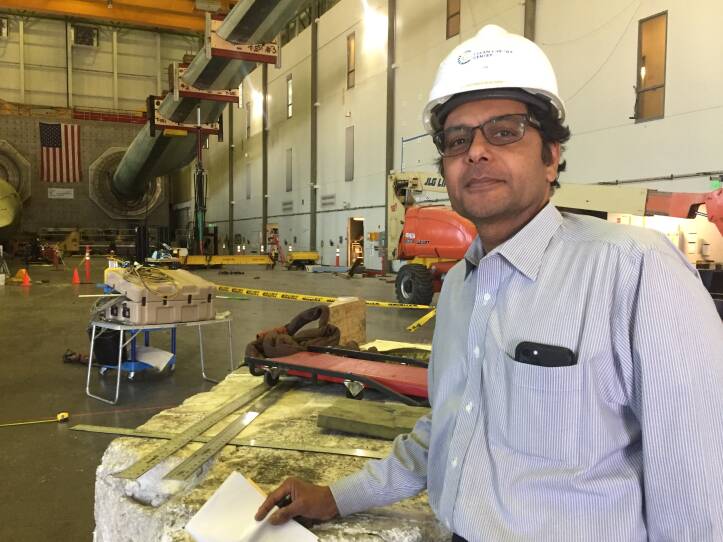
“You're seeing a utility-scale wind turbine blade being structurally tested,” he said. “So it's moving up and down. That's what it would do at fully rated wind speed, when it's producing the rated power.”
The silver-gray color makes the blades look like metal, but they’re not.
To be as light as possible, they’re made of thin layers of fiberglass and balsa wood, fused with resin. They’re hollow, reinforced inside with fiberglass bracing.
Before this, the blade went through weeks of static testing — casually known as the “crash test.”
That’s when the lab puts a really big load on the blade, simulating a 50-year wind gust, to make sure it doesn’t break.
“And sometimes, for research purposes, we keep going until the blade breaks,” Yarala said. The idea is to tell the manufacturer how wide the safety margins are. “We're breaking it on purpose, to learn about it.”
Time to build
Once the components have been put through their paces, and the permits and contracts signed, it’s time to build.
America’s first major offshore wind farm, Vineyard Wind, will have 62 turbines. Workers are laying undersea cables now, and the turbines are scheduled for installation next summer, 15 miles south of Martha’s Vineyard.
Offshore wind is so new in the United States that the installation process is still being worked out.
For one thing, a century-old law called the Jones Act says maritime shipping between any two points in the United States has to be done with a U.S.-registered vessel.
And a wind farm counts as a point.
But, as Vineyard Wind CEO Klaus Skoust Moeller points out, carrying turbines out to a wind farm with a U.S. vessel isn’t possible yet.
“There's no big installation vessels actually available in the U.S.” he said. “We don't have any because they don't exist, right?”
Right.
Instead, they’ll use a Danish vessel — aptly named Sea Installer.
Rather than carry the turbines itself, as these vessels do in Europe, it will have to stay at the wind farm while American barges ferry out the components.
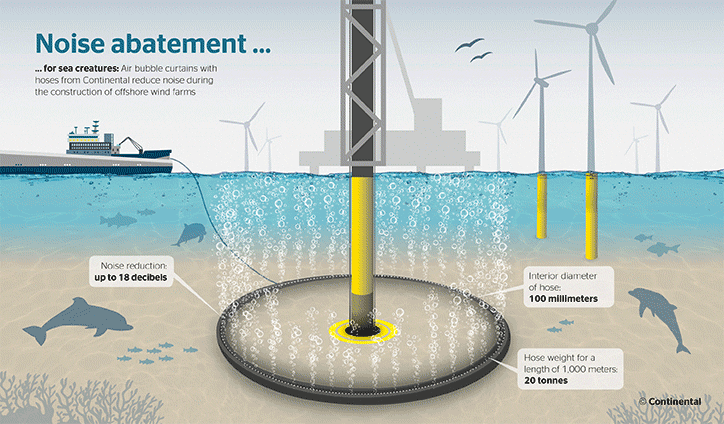
But let’s back up — because what disrupts marine life the most during construction is driving the foundations into the seabed.
Moeller said they’ll use a bubble curtain — a wall of air bubbles — to reduce noise.
“It's basically just a hose that blows bubbles in the water that makes the noise lower,” he said.
The turbine components for Vineyard Wind will come mainly from Europe on what’s called a heavy-lift vessel, designed for extra weight and bulk.
Towers are shipped in sections and assembled at the staging port — in Vineyard Wind’s case, New Bedford.
Life on the installation boat
Martin Lind Hansen is head of offshore construction in the United States for Siemens Gamesa, a turbine manufacturer supplying other projects on the East Coast.
He said 12 to 14 people live and work on an installation vessel.
“The living quarters [are] actually quite nice,” he said. Two crew members share a room, but work different shifts, “with every convenience possible — television, phone systems, etcetera, etcetera.”
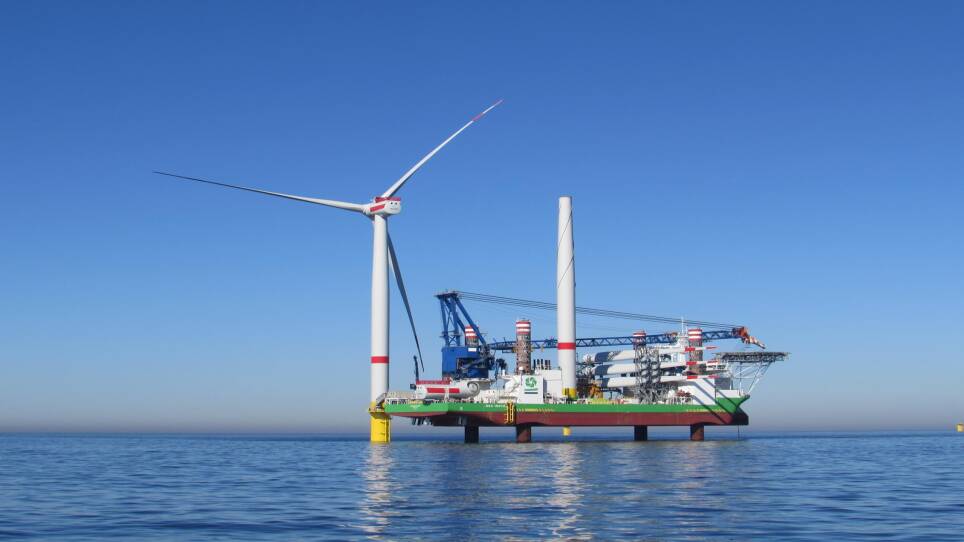
They get three meals a day. They work 12-hour shifts and spend two or three weeks on the ship before rotating off.
“You have your laundry done during your rotation. And basically, the only thing you need to worry about is to get up in the morning, or whenever your shift starts, and be ready,” he said.
The boat is a jack-up vessel, which means it can jack itself up on four legs, raising the hull out of the water to create a fixed platform.
A crane with different attachments, called yokes, picks up the offshore wind towers, nacelles, and blades and lifts them into place.
The nacelle is the mechanical heart of the turbine, containing the drive train and generator.
Hansen said workers need to have broad knowledge to do this kind of installation.
“They will attach all the bolts and make sure that it's secured,” Hansen said. “Then, they'll take off the lifting equipment, and then the nacelle will be electrically and mechanically finalized by these technicians who [are] already in the tower.”
The blades go on last.
With hundreds of turbines planned for the East Coast and the health of the planet at stake, Hansen said it seems like everyone involved feels proud of what it means.
“It is something very unique to be a part of,” he said. “It's a significant push towards a greener future for America.”
And after all that planning, the crew can install a turbine every 24 hours.